Round Slings vs Web Slings - Rigging 101
When the time comes to perform an overhead lift, there are multiple sling options available in the market that can get the job done. In fact, we’ve discussed the two most popular ones in our previous blog Advantages and Disadvantages of Wire Rope Slings vs Chain Slings. However, there are some criteria that these key products struggle to meet which can be addressed with either round slings or web slings depending on the task at hand.
In this article, we will discuss the advantages and disadvantages of these two synthetic slings to help you determine which one might work best for your application, while also keeping in mind all the key factors in your lifting plan.
What are Round Slings?
Round Slings, sometimes referred to as Endless Slings, are made of continuously wound high-performance polyester yarn encased in a tubular single-ply or double-ply Polyester cover. Often identified by colour, the cover usually gives a visual indication of its rated capacity while shielding the internal yarn from external threats.
Round slings are versatile, lightweight, and offer superior load protection for sensitive materials and finished parts.
Advantages of Using Round Slings
- Perfect for lifting round loads such as tubes or piping (especially in choker hold)
- Colour coded outer cover allows for quick identification of the sling’s specifications
- Important: these cover colours are not industry regulated; consult the product tag or the manufacturer’s colour/rating guide for details. If unsure, contact the manufacturer directly for assistance.
- The outer cover protects internal yarn from abrasion, grease, and UV rays
- Easy to inspect for physical damage
- Portable
- Offers protection of delicate loads
- Has higher lifting capacity than Synthetic Web Slings
Disadvantages of Using Round Slings
- Cannot be used in extreme temperatures (-40°F / 194°F); susceptible to heat damage
- Not suitable for alkaline environments (e.g. mineral, coal, acid mining)
- Must be stored in a cool, dark place to protect them from UV damage
Round Sling Inspection: Failure Criteria
When inspecting a Round Sling, it is important to be able to identify common signs of damage and misuse. Inspecting your sling before every lift helps to ensure the longevity of the sling, the safety of those around the job site, and the protection of the load being lifted. Key warning signs that your sling needs to be pulled from service include:
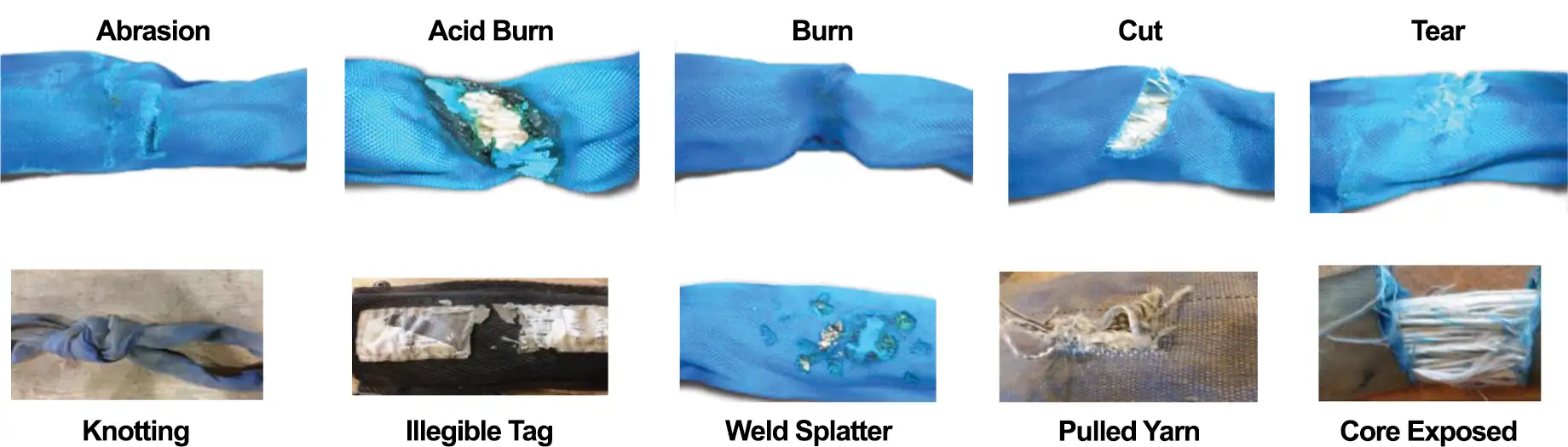
Abrasion damage occurs when a round sling encounters a rough surface with enough force to wear down the protective sleeve, potentially exposing the inner fibres.
Acid Burns damage the outer jacket of both Nylon and Polyester slings; if a strong enough acid is involved it can expose the inner fibres and damage them.
Burn Damage occurs when a sling is exposed to temperatures exceeding 194°F. Because they are made of synthetic materials, exposure to heat at this level will cause them to melt.
Tears and Cuts occur when a sling is not properly padded for a load, causing excessive tension to be placed on a small portion of the sling, potentially ripping the outer sleeve and internal yarn.
Knotting causes unequal distribution of tensile force around the knotted area reducing the Working Load Limit (WLL). The same concept is applied when calculating the rated capacity of a sling in a choker hitch. Because there is an increase in tensile force at the point of the choke (or the “knot”), the slings WLL is reduced to account for the extra strain. It is important to note that you should never tie a knot in a sling to adjust its length.
Illegible Tags indicate that some or all details on the sling tag can no longer be identified properly. Equipment being used for overhead lifting should always be tagged with specs to ensure the right sling is being used based on the lift requirements. There should never be any guessing involved when selecting a sling.
Weld Splatter is harmful to Round Slings because the jacket and fibres are not resistant to heat. The presence of weld splatter indicates that the structural integrity of the protective sleeve, and possibly the internal fibres, could be compromised.
Pulled Yarn indicates that the sling may have been exposed to a shock load, damaging the internal fibres.
Exposed Core is easy to identify with a visual inspection. If you can see the core (yarns) of the sling, it must be removed from service.
Round Sling Working Load Limit Cheat Sheet
MacMor’s Macline brand offers a robust selection of Round Slings to meet the needs of any lift with lifting capacities up to a whopping 40,000 lbs in a vertical hitch.
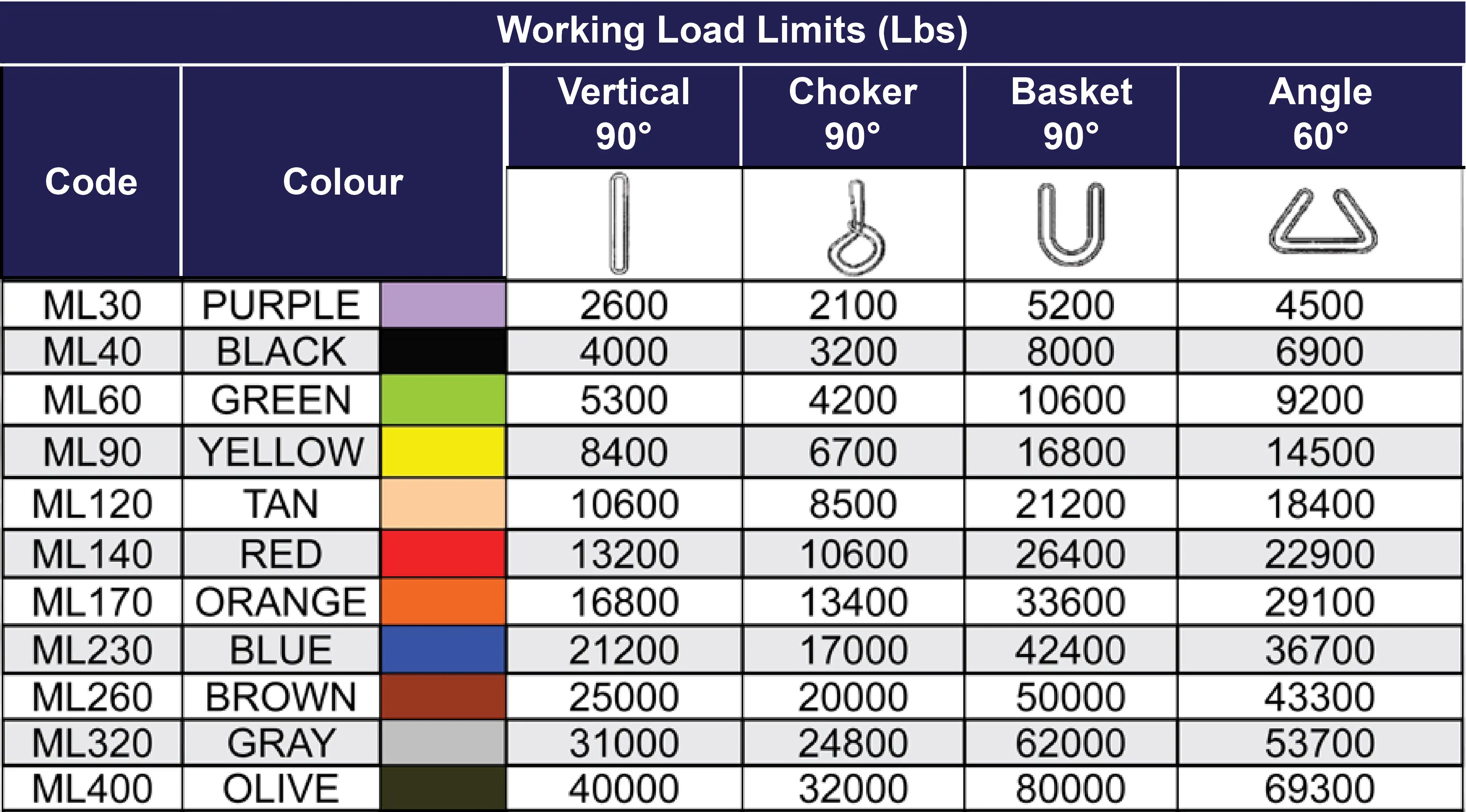
Web Slings
Web slings are flat straps made of Nylon or Polyester that typically have flat or twisted eyes on either end. They are used in a variety of applications due to their affordability, versatility, and ability to tightly secure delicate loads without causing damage.
Advantages of Using Web Slings
- Inexpensive when compared to other sling types
- Flexible; easily wraps around almost any shape load
- Tightly secures delicate loads; protects from scratches or damage
- They are lightweight and easy to handle; high strength-to-weight ratio
- Resistant to certain chemicals (see graphic)
- Not affected by grease, oil, and moisture
Disadvantages of Using Web Slings
- Synthetic Web Slings have poor abrasion and cut resistance
- Requires padding to be used on corners and rough surfaces
- Limited attachment points
- Low heat resistance; temperatures above 82.2°C (180°F) damage both Nylon and Polyester slings
- Wet or frozen slings will have a reduced WLL
- Susceptible to UV damage over long exposure; must be stored in a cool, dry, dark place
Nylon vs Polyester Web Slings
If you’re thinking that synthetic web slings might be the right choice for your application, you’ll be happy to know there are 2 materials used to construct them: Nylon and Polyester. Although they are generally quite similar to each other, there are some differences that should be mentioned.
Between the two fabrics, Nylon is best known for its strength and higher stretchability over polyester. This stretching, although minimal, is due to Nylon’s ability to absorb moisture, which also happens to make it less capable of retaining colour dyes when exposed to UV. Although both resistant to mold/mildew, Polyester is more often recommended for any outdoor projects because of its improved resistance to UV and pilling in comparison to Nylon.
The chemical resistance chart below highlights the compounds that Nylon and Polyester can (or cannot) be exposed to:
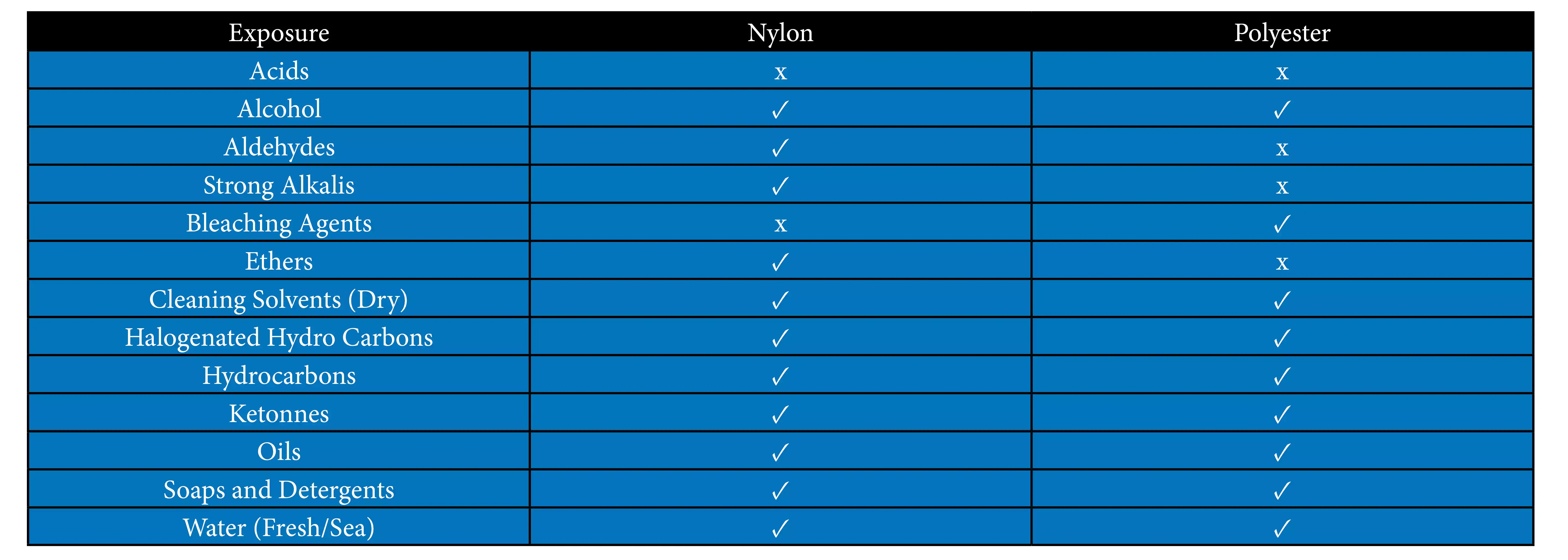
Web Sling Inspection: Failure Criteria
As previously stated, it is important to always inspect your rigging equipment before use. Every time a sling is used in the field, its strength and resilience is being tested, which makes any pre-existing damage to the sling a safety threat. Keeping this rule as a “best practice” will ensure every time you perform a lift, the sling operates with maximum capacity without the threat of causing injury or damaging your load.
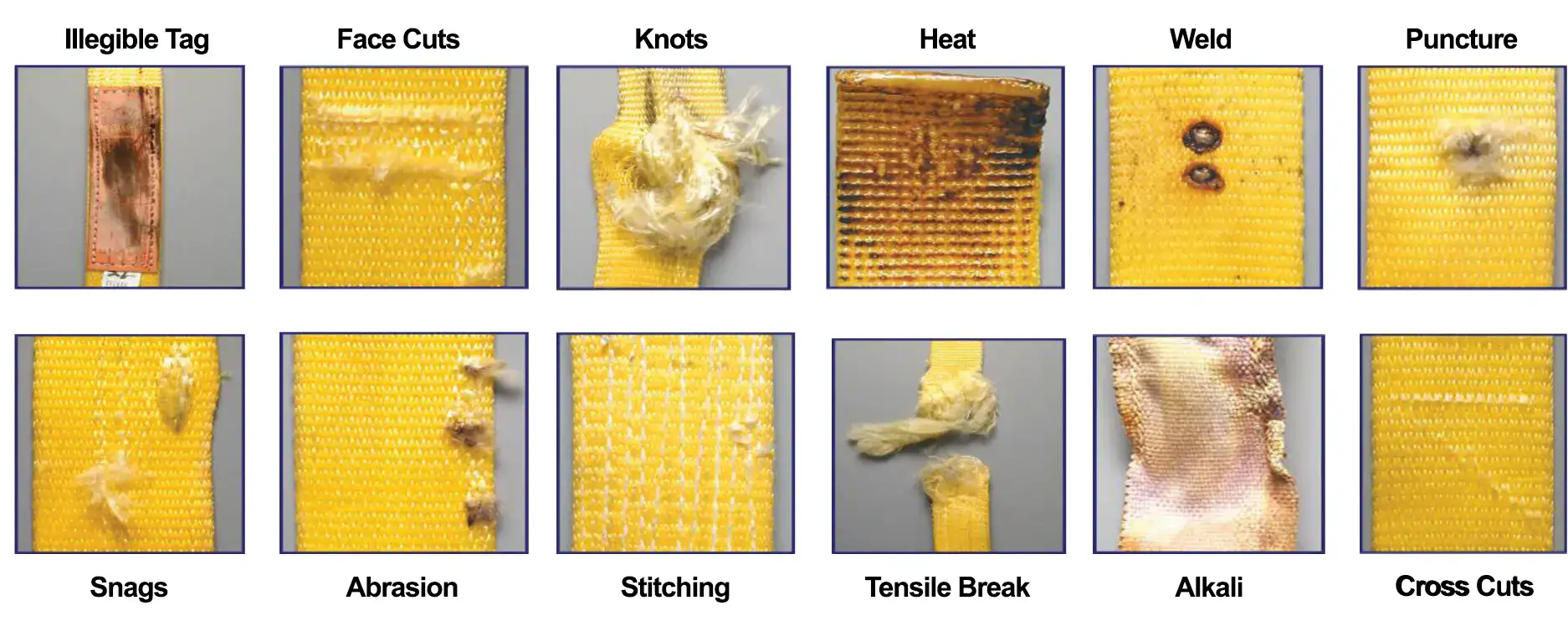
Illegible Tags indicate that some or all details on the sling tag can no longer be identified properly. Equipment being used for overhead lifting should always be tagged with specs to ensure the right sling is being used based on the lift requirements. There should never be any guessing involved when selecting a sling.
Face Cuts occur when the surface of the sling is exposed to abrasive or sharp materials causing cuts to surface-level threads.
Knots cause unequal distribution of tensile force around the knotted area reducing the WLL. The same concept is applied when calculating the WLL of a sling in a choker hitch. Because there is an increase in tensile force at the point of the choke (or the knot), the slings WLL is reduced to account for the extra strain experienced at that point.
Heat Damage occurs when the sling is used in environments with temperatures exceeding 180F.
Weld splatter can burn and singe all types of synthetic slings. This splatter can prevent a sling from elongating normally under load, causing tension points destined for failure. Weld splatter also destroys the surface layer fibres it is exposed to which greatly affects the WLL of the sling.
Punctures occur when sharp objects penetrate the sling. Signs of punctures are a clear indication that the sling should be removed from service.
Snags occur when a sling gets caught on a sharp object or corner causing threads to be pulled from the surface of the sling. This will often result in a lower WLL, making it unsafe to use.
Abrasion occurs when a sling connects with abrasive surfaces and gets worn down at the point of contact.
Stitching is present in the eyes of web slings. This is used to join the webbing into one cohesive lifting sling. Damage around these areas can cause the eye of the sling to become compromised.
Tensile Breaks occur when a sling under load experiences a sudden elevation change, causing the sling to experience a rapid change in tensile force at specific points of the sling. It is for that reason that when slings are pull tested, they are pulled with gradually increasing force to mimic the proper technique of a lift.
Alkali Polyester Slings should never be used in Alkaline environments. If you’re looking for a lifting solution suited for Alkaline environments, Nylon Web, Chain, or Wire Rope Slings are your best option assuming they work with the conditions of your lift plan.
Cross Cuts indicate the sling had contact with an abrasive or sharp surface that cut through the sling. While sometimes the damage can appear minimal or simply cosmetic, it is important to note that the slings areis rated based on theirits full strength with all threads intact. Any indication evidence of cuts across the fabric should alert you that the sling should be is an indicator that the product should be removed from service.
Web Sling Working Load Limit
MacMor’s Macline brand offers a robust selection of Round Slings to meet the needs of any lift with lifting capacities up to a whopping 40,000 lbs in a vertical hitch.
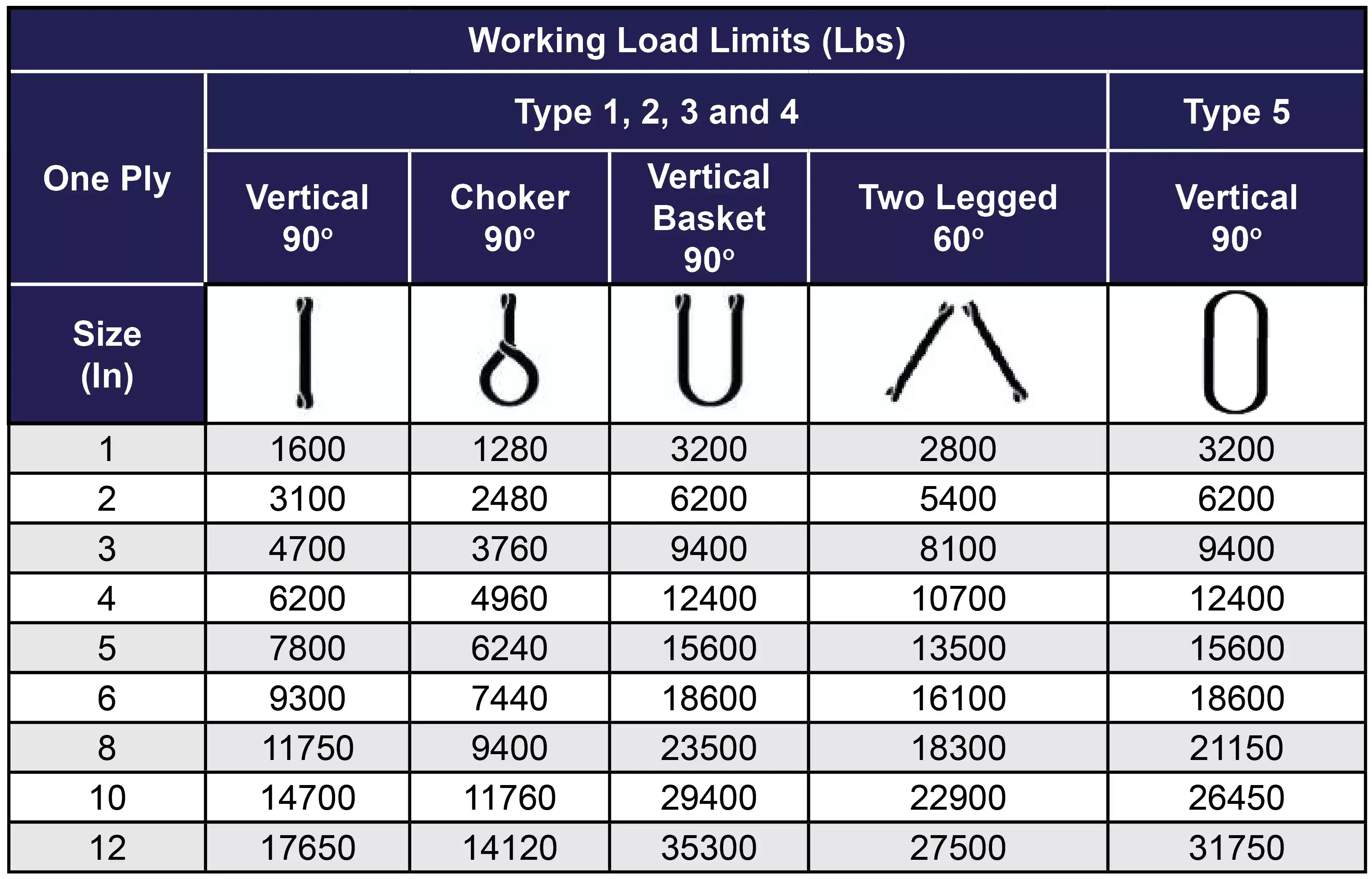
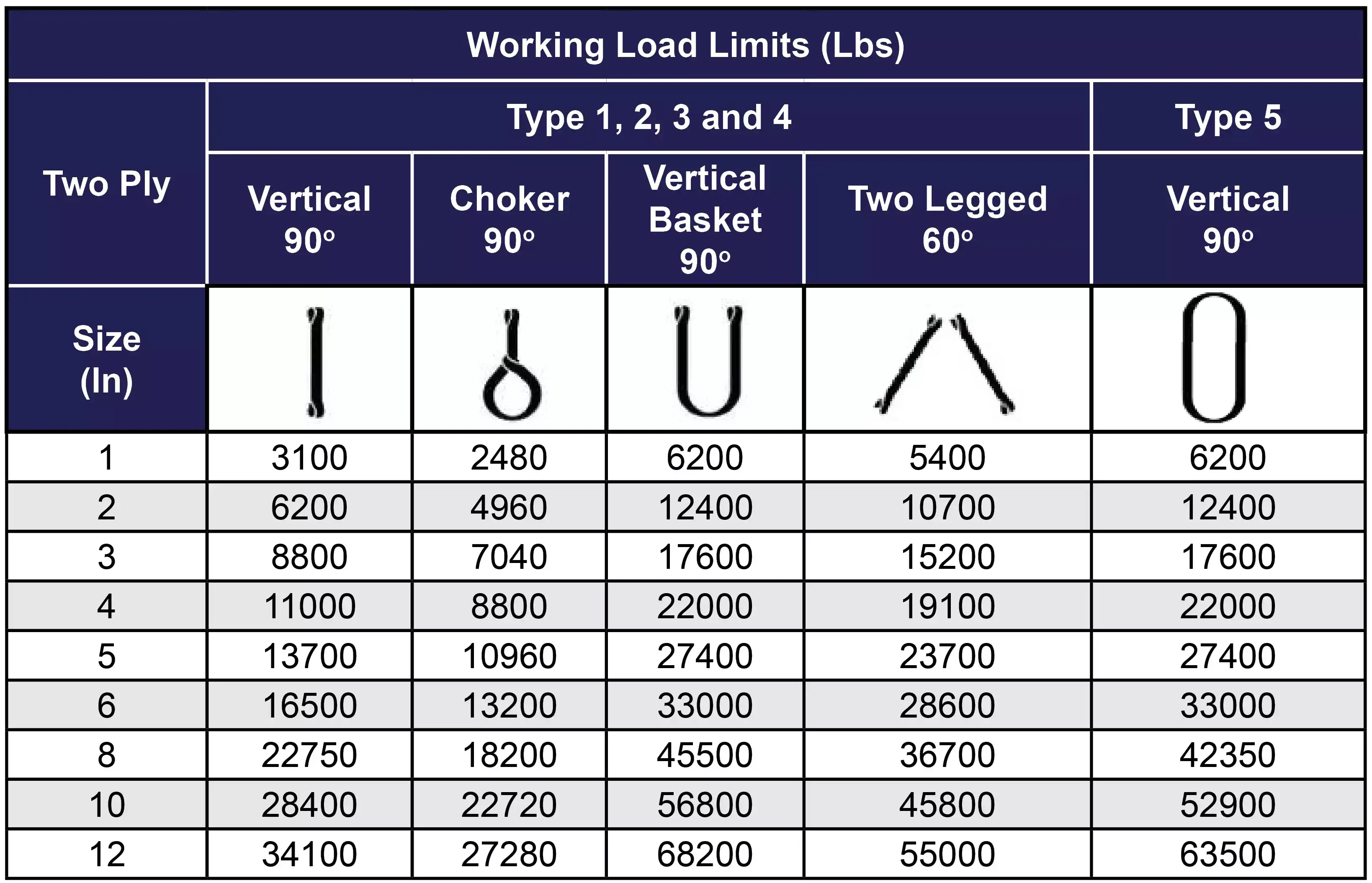
Summary
Web Slings and Round Slings offer a lot of the same benefits and are very versatile. They’re lightweight, flexible, and easy to work with, which is why they are preferred in a variety of applications.
MacMor Industries is your one-stop-shop for lifting and rigging solutions, Training, Proof Testing, Inspections/Repair, and Certification. If you require help or guidance in developing a rigging solution, please do not hesitate to contact us. One of our Rigging Specialists or Sales Representatives will be more than happy to work with you in developing an assembly that meets your needs.
Like the Blog and Video? Please consider sharing it with your friends and your team.