Glove Coatings 101: How to Choose the Right Synthetic Glove Coating for You
Welcome back to Feature Friday! Today, we’re going in depth on another popular topic about the gloves we offer at MacMor: Synthetic Glove Coatings. If you haven’t read our previous blogs about gloves, you can check out where we talk about the Watson Van Goat Gloves, various winter glove liners, leather versus synthetic gloves, and a deep dive on leather gloves.
Key Notes About Glove Coatings
In general, coatings are applied to safety gloves to improve their performance and protective capabilities. There are countless variations of glove coatings in the market, and each one is designed with specific tasks in mind. For example, if you want resistance to a wide range of chemicals, you will typically look for a PVC coating on your gloves for its ability to withstand exposure to a wide range of chemicals, and its overall thickness and durability. On that note, it should be mentioned that gloves with more durable coatings are typically more expensive (all else being equal), but there are various other factors that normally come into play that will affect pricing.
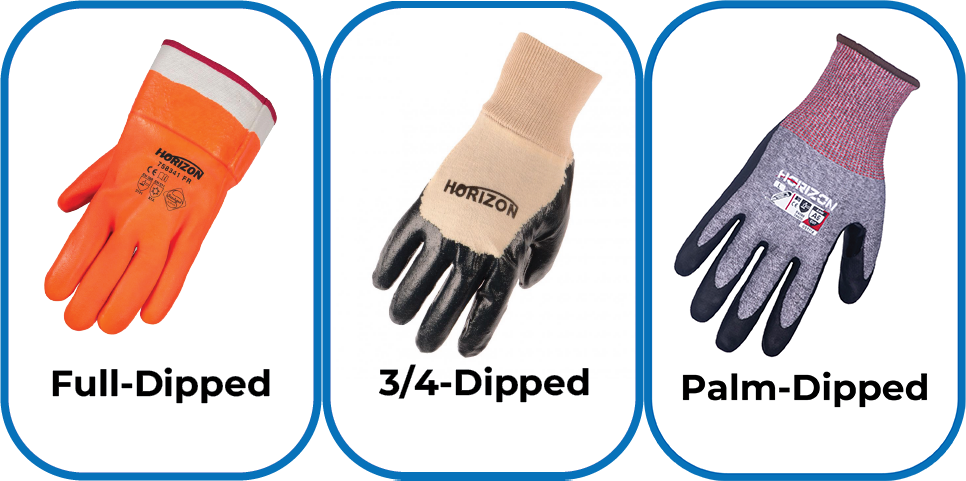
It’s important to select the appropriate glove to help mitigate the risk of injury in the workplace. While workplace hazards are inherently dangerous already, what makes them even more threatening is when workers don’t wear hand protection, either because the gloves are uncomfortable, too bulky, or in some cases, they’re having a reaction to the coating.
Latex Coated Gloves (Smooth/Crinkled/Textured/Foam)
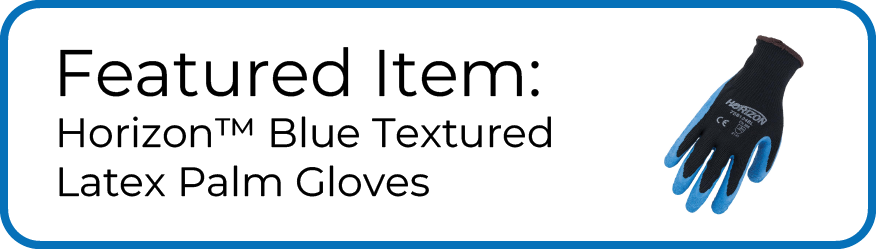
Latex-coated gloves are typically available with smooth, crinkled, textured, or foam coatings. No matter how the latex is applied, latex coated gloves provide exceptional grip and dexterity in both wet and dry applications. The crinkle texture, as shown in the Horizon™ gloves above, provides additional abrasion resistance as well as an enhanced grip.
Latex coatings are also flexible and durable in a wide range of temperatures, making them an ideal coating for various types of winter gloves. You’ll often find latex coated gloves on construction sites and in manufacturing facilities.
Of course, one of the major drawbacks for latex is that it is a common allergen. It also has limited chemical resistance to organic solvents and hydrocarbons.
Smooth Nitrile Coated Gloves
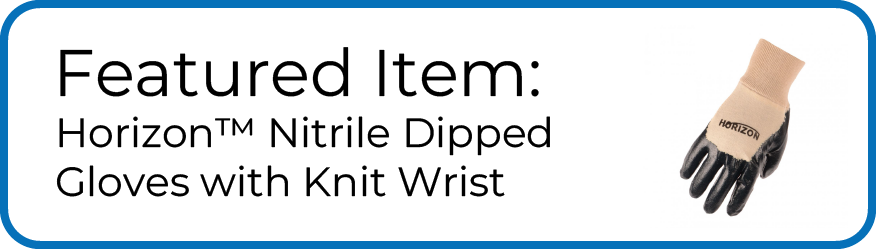
One of the most popular coatings in the market and a great alternative for those with latex allergies, nitrile coated gloves provide similar attributes and protection to latex coated gloves.
Nitrile coatings generally fall into two categories: Smooth (flat) or Foam (sandy).
Smooth nitrile coatings are much more durable than their foam counterparts, while also staying relatively thin. Gloves with this coating are perfect for tasks that require dexterity and precision, such as assembly line work or electronics manufacturing.
They provide excellent grip, but strictly in dry applications since smooth nitrile repels oil and water. So, if you’re working in a wet environment or handling oily parts, you’ll likely struggle with grip when using gloves with this smooth coating. Thankfully, there’s a solution for that.
Foam and Micro-Foam Nitrile Coated Gloves
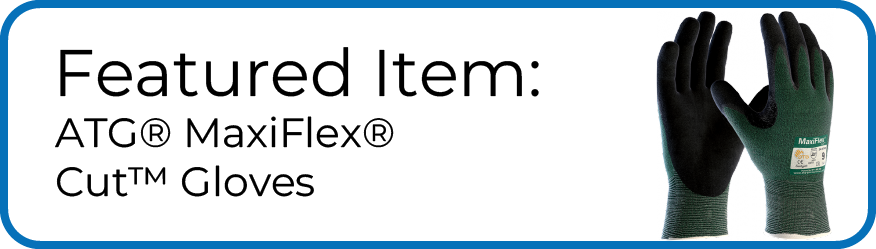
What sets foam nitrile coatings apart from their smooth counterpart are the small, porous bubbles on the surface. The bubbles essentially add small pockets for oils to get absorbed by the glove, allowing you to work in oily environments without compromising grip. Micro-foam nitrile simply has smaller bubbles, allowing the coating to be thinner for better breathability and dexterity, all while remaining impressively durable.
Workers in construction, automotive, or warehousing benefit greatly from gloves coated with micro-foam nitrile.
It’s important to note that because of their breathability, foam and micro-foam nitrile coated gloves are not designed for extensive or prolonged chemical exposure. Overall, we can comfortably say that foam and micro-foam nitrile are some of the best coatings in the market, which means gloves with these coatings tend to be a bit pricier.
PVC Coated Gloves
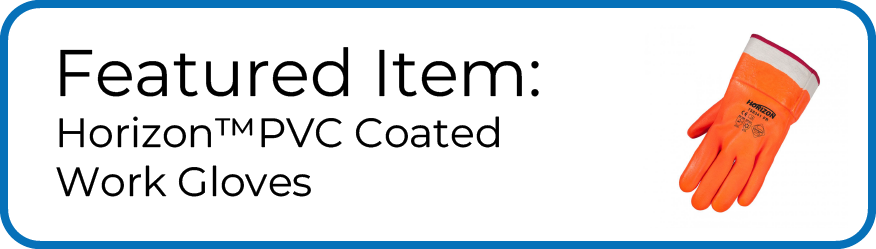
Gloves with PVC coatings offer an outstanding resistance to a wide range of chemicals, including acids and caustics. PVC coatings also keep their flexibility even in cold temperatures, making them a popular choice for a lot of cold-weather applications.
The thick material also makes PVC coated gloves excellent for withstanding mechanical abrasions, light cut hazards, and basic puncture risks. That said, because PVC coatings are naturally thicker and bulkier, you’re trading dexterity and precision for toughness and durability.
Polyurethane Coated Gloves
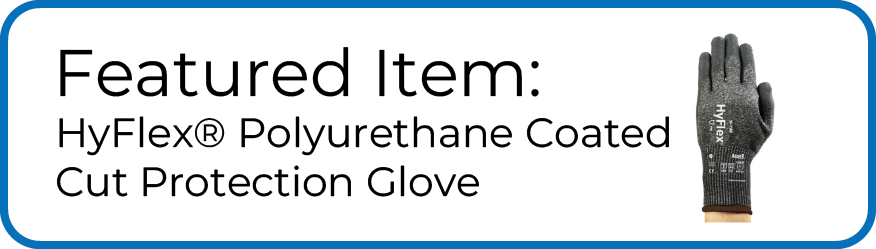
Polyurethane coatings are some of the thinnest in the market, almost feeling like a second skin, which means gloves with this coating tend to have fantastic dexterity and tactility. They have similar traits to foam nitrile coating for permeability and improved grip in oily environments.
At MacMor, we rarely keep polyurethane coated gloves on the shelf because most of these gloves carry trace amounts of Dimethylformamide, or DMF, which is carcinogenic solvent. DMF is needed to properly adhere the coating in a solvent-based reaction. While most of the DMF is washed away during the manufacturing process, these trace amounts can still be left behind in the glove which can then be absorbed through the skin.
There are polyurethane coated gloves that don’t rely on a chemical reaction with DMF, but they’re few and far between and usually at a higher cost. A way to tell if a polyurethane-coated glove is DMF-free is by looking inside the glove; if the polyurethane seeped through the fabric, the coating was applied using a solvent-based reaction and may have traces of DMF.
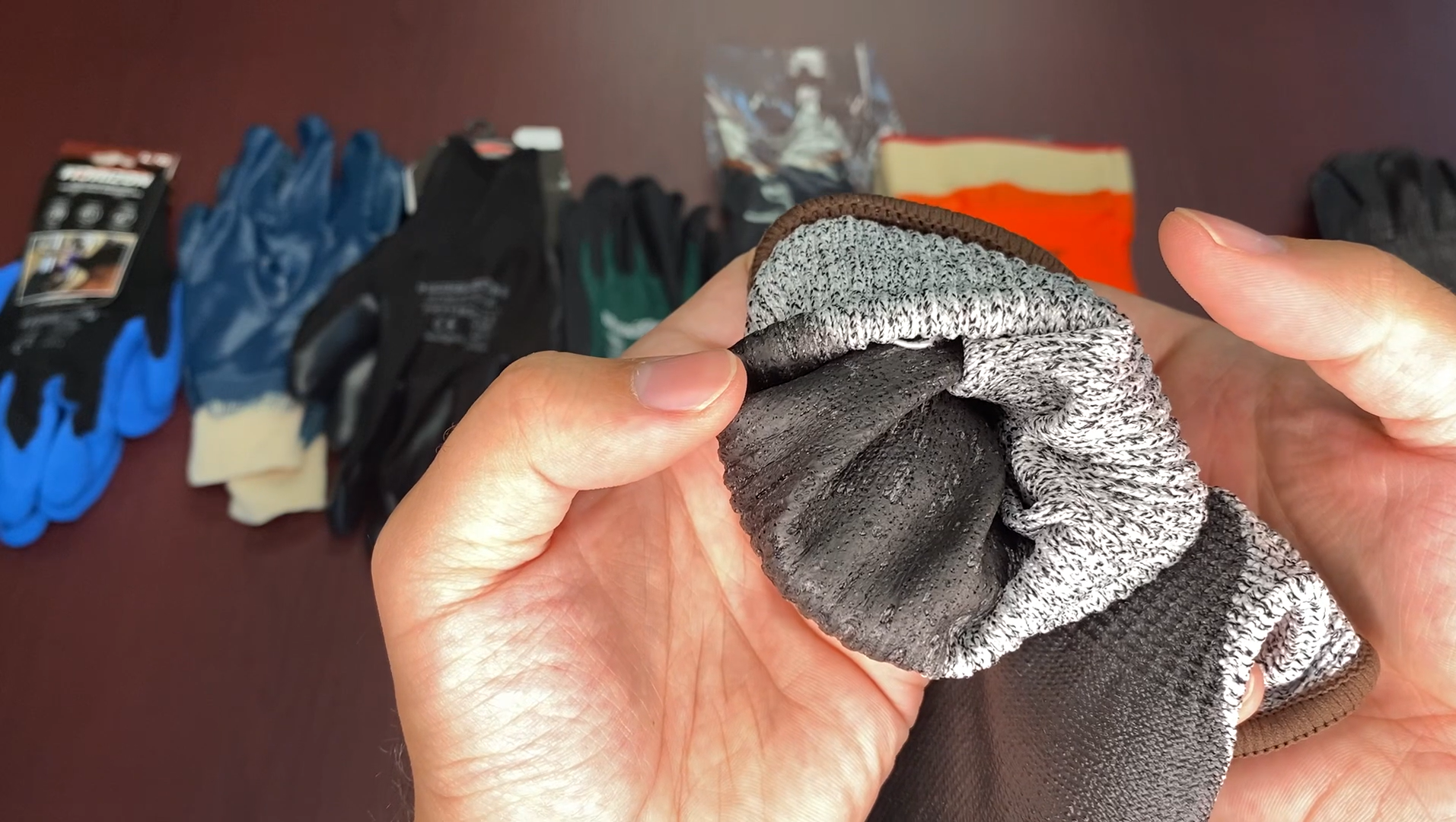
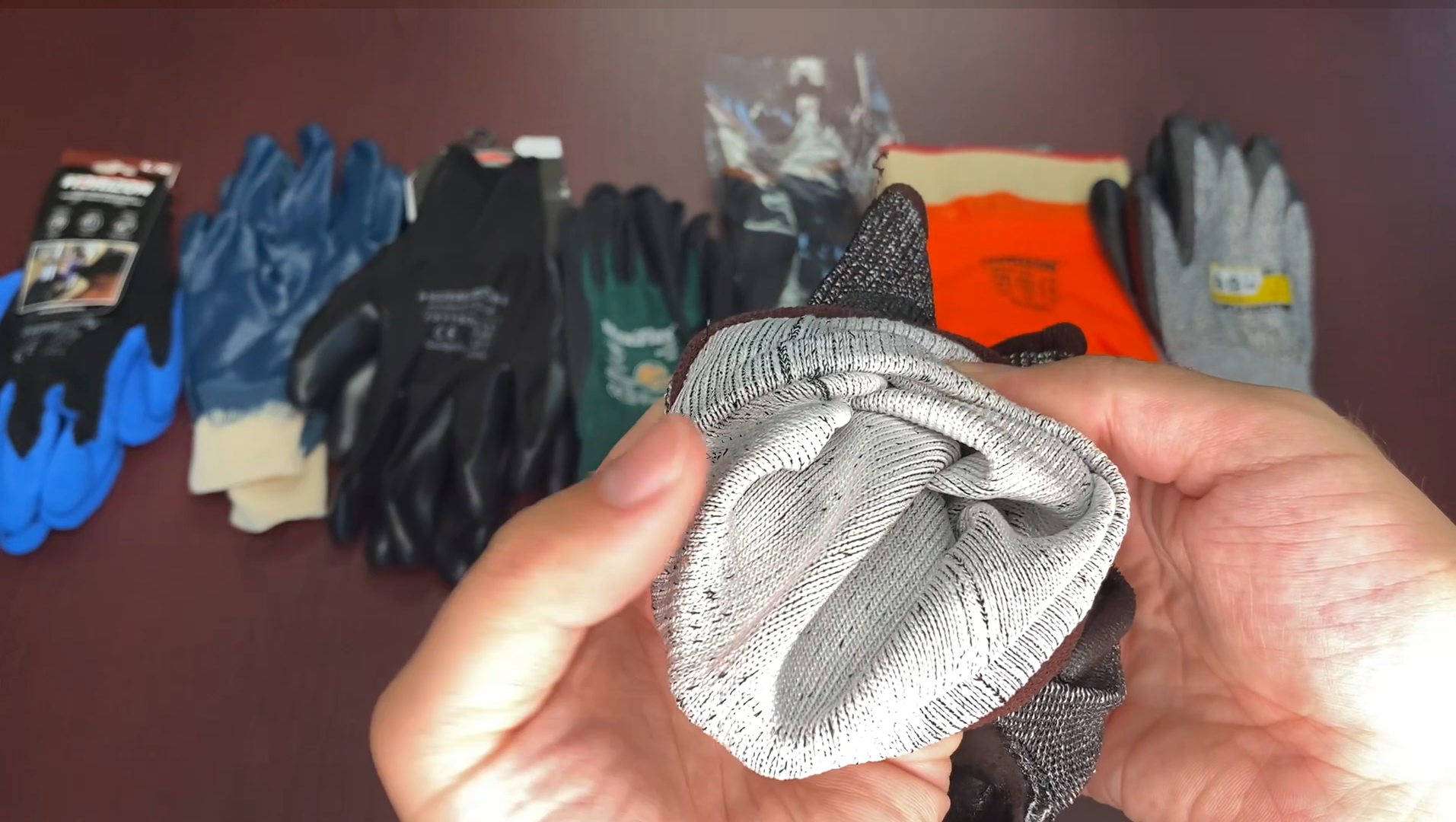
At the end of the day, the right glove coating will not only help with your tasks, but also increase your level of safety and productivity.
Keep in mind that these are just some of the common glove coatings you’ll typically find in the market; this is not an exhaustive list of every variation that exists.
If you’re still not sure what glove is right for you, MacMor offers glove audits to ensure the proper gloves are being used for the application. We partner with some of our vendor reps to work with you to evaluate your specific needs and offer solutions we think will work best within your budget. If this interests you, don’t hesitate to contact us today.